NRRA Newsletter: February 2017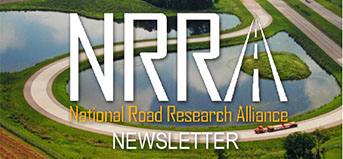
NRRA Associate Call to Action
A Blueprint for Implementing Road Research
By Dan Schellhammer
I don’t have to tell you how important it is to make the journey from verified research to implementation in the field. It is, for our industry and this alliance, where the rubber meets the road. With MnROAD and other projects, we seem to be pretty good at researching innovative approaches and proving they work. That doesn’t, however, always translate that well into the field where real projects are happening.
It can be frustrating, because we all know that there are great innovations in paving happening—innovations that can save money, extend the life of our roads and help the environment. However, we don’t always see these innovations migrating to work sites and large-scale paving projects.
We need a blueprint for implementation. Here are some the elements of the blueprint that we, as an alliance, need to start working on.
Steps
We need a system that goes into effect once research is completed, verified and ready for the field. This should be a step-by-step process with as much detail as possible. We can’t just publish the research and hope someone finds it and uses it. Each completed, verified research project should be fed into a workflow system that will bring it to implementation. Naturally, these steps need to be worked out in a collaborative effort with state agencies and contractors.
Acceleration
Innovation does happen, but we need to ask ourselves if it can’t be accelerated? State agencies like DOT’s are careful, and that’s good, but we need to ask ourselves the hard questions about caution versus progress toward our shared goals. In all cases, I am talking about verified research, so being cautious should be tempered by the fact that these are proven technologies.
People
Any blueprint must take into account the human factor, i.e. human resistance to change. Doing “things the way we always have” still gets in the way of implementation, even when those particular words aren’t spoken aloud. The four human factors the NRRA needs to address, as I see it, are:
- Leaders who want innovation to happen need to make it happen.
- The people who can act on innovation need to have the right information.
- Incentives need to be built into people’s job descriptions so they are accountable for innovation.
- Design questions need to be answered in advance, not at the job site.
Training
Knowing what to do is always dependent on knowing how to do it. If people like inspectors don’t have the training for a new technique, it can be a significant speed bump. Just having specs in a manual isn’t enough. We need training modules or webinars (or both) built into any blueprint for implementation.
NRRA’s Tech Transfer Team
Training may be one area where NRRA’s Technology Transfer Team gets involved. This team’s charter is specifically to get people comfortable with best practices and innovative pavement technologies. It makes sense, then, that the Tech Transfer Team would look at developing training in the form of seminars, workshops, online training modules and anything else that would help push implementation.
This is not a comprehensive list of what needs to go into an implementation blueprint, but it’s a good start. The NRRA is poised to make great headway in the area of implementation. I will be eager to hear from you all at the Pavement Conference in May about what else needs to happen to make implementation happen.
Dan Schellhammer, P.E., is Vice President of Midstate Reclamation and Trucking, Inc. in Lakeville, MN. Midstate specializes in the recycling of asphalt pavements and stabilization of in-place materials.
If you are an associate member and have a call to action for the pavement industry, please contact us with your ideas.
Research Pays Off—Upcoming Topics
Road Research provides a monthly seminar to highlight research topics that will make an impact on the work done as part of the National Road Research Alliance. Join us on February 21 at 9 a.m. (CST) for a webinar called “Barriers to Implementation of In-Place Recycling.”
Please tell your co-workers and colleagues about this series and encourage them to join us. Past attendance has been weaker than we had hoped. This series is, by definition, a valuable resource that actually has dollar figures attached to research results.
Save the Date
Remember that May 24 is our Pavement Conference.
Research Pays Off will be scheduled for the third Tuesday of the each month. Possible upcoming topics may include:
- Feb - Barriers to Implementation of In-Place Recycling
- March - Minnesota use of Geogrid and current advancements
- April - National Road Research Alliance Long Range Research Plans
- May - MnROAD/NCAT Pavement Preservation Study
Do you want a specific topic covered? Do you want to present on a topic? Let us know. And don’t forget to sign up to get on our email distribution list.
TRB Meet and Greet
Thanks to everyone who dropped by for our Meet and Greet at TRB last month. |
The National Road Research Alliance sponsored a Meet and Greet at the TRB conference on Wednesday afternoon (Jan. 11), and we want to thank you all for showing up. We had between 25-30 people asking questions and making suggestions about how to improve the alliance. Some of the questions we continue to receive are:
What is the pooled fund?
It is the combined money from all the NRRA memberships plus the additional money kicked in by MnDOT. Becoming a member means you become part of the pooled fund and you get to tap into the enormous resources of our growing alliance.
What do you get if you join the NRRA?
You get access to one of the leading pavement research centers in the nation--access that translates into opportunities to do your own research and learn from the research other states are doing as part of the alliance. In addition, you get access to the Pavement Conference, our newsletter, our Facebook site, our YouTube channel, our twitter feed…the list continues to grow. Most importantly, you become part of an alliance of states and associates who have joined forces to make a more durable, economical and sustainable future for our roads.
What are we currently doing out at MnROAD?
This spring, we will be constructing new test cells at MnROAD. We are also working with NCAT on monitoring test cells both here in Minnesota and in Alabama. Find out more about MnROAD. You will be impressed.
Is it too late to get a project in the queue?
No, it’s not too late. The NRRA is in this for the long run, and we are continually planning new research for new cells. Help us plan for the future by joining the NRRA.
Getting the whole pavement picture
By Shongtao Dai and Kyle Hoegh
MnDOT’s Vision: Implementing quality control and assurance using continuous and full coverage methods.
When paving with asphalt mixtures, obtaining target density is the goal. As you know, the density of the pavement we put down is affected by different factors, such as the mixture temperature and the roller compactor operations. We have some great ways to measure mixture temperature and roller compactor operations both using IR (infrared) sensors and IC (intelligent compaction) as the pavement goes down and gets compacted. Measuring the final result, however, is currently based on limited coring of the pavement at random locations that give an incomplete assessment of the achieved density.
![]() |
Air void data gathered by GPR |
During the last decade or so, the pavement community has worked with ground penetrating radar (GPR) manufacturers to make great progress in designing and implementing GPR for pavement applications. The product of interest for this article is a rolling density meter (RDM) which resulted from a SHRP2 R06C study. The RDM is based on high-frequency air-coupled GPR antenna that gives us a view of relative pavement compaction at a greater coverage that is truly game changing, and we have been taking it out of the testing environment into full-scale investigations on real projects with great results.
MnDOT has conducted several field studies and shown that the RDM can determine relative compaction levels nondestructively. MnDOT’s Office of Materials and Road Research has developed a statistical analysis method, similar to the percent within limit method, but with more pavement coverage, that can be used to assess compaction quality including the longitudinal joint.
Here are ways GPR improves on the processes of the past.
Complete picture
The standard way to measure the density of a project is, and has been, accomplished by drilling a core in random spots along the project and measuring the core in an off-site laboratory. Of course, if the project wasn’t reaching the required density, the core would tell you about it a few days later. That is too late to make any adjustments to the paving project, so it was a very reactive approach to measuring. Because you were taking such a small sample and hoping it was representative of the whole project, you often ended up with information that was both too little and too late.
![]() |
Out on the road with GPR |
With GPR you get a continuous and full-coverage view of the project in terms of compaction level and uniformity, rather than just a random sample. You get a complete map of the whole pavement including data that assesses the final achieved results of the entire paving operation--asphalt mix, placement and compaction efforts that led to the final air void content of the mat.
Instant Feedback
Remember what we said about density information from cores taking days? With GPR, the paving operation can get instant feedback on the project and can be used to inform adjustments to both the mix and the compaction equipment (and compaction patterns) right away.
This kind of instant, complete data is an important step to reaching optimal density for your paving project. It is already changing the way we look at paving projects, and it will probably change the paving industry substantially as it rolls out.
Smart Coring
We have already mentioned that traditional density measurement techniques involve randomly selected areas of pavement where cores would be drilled. Contractors have to sort of trust on faith that the cores you drilled were representative of the whole paving project. With GPR, you can still do cores, but the density map will allow you to intelligently select where the cores will be taken. Your GPR map might be showing you a patch that has a lot of air voids. You can then take a core on that patch to see what went wrong—mix, compaction or something deeper.
Seeing the Unseen
MnDOT used GPR for asphalt compaction assessment on two real-world projects in the summer of 2016: Hwy 14 and Hwy 52 in our Rochester district. On one of the projects, Hwy 14 project in south central Minnesota, the GPR successfully detected that the density of the whole project was increased from 93% to 94%--simply by adjusting the roller pattern to get better compaction. While cores later corroborated this finding, the GPR was able to detect and communicate that the new rolling pattern caused an increase in compaction on-site the same day the new pattern was implemented.
By the Numbers
Density matters. While the effect of increased density on pavement life depends on changing site and other conditions from project to project, studies cited by a recent NCAT project showed fatigue life increasing at a range of 8% to 43% from project to project for each 1% increase in density. To put the potential impact of the on-site feedback from RDM into perspective, let’s take the Hwy 14 example: GPR was able to identify the optimal rolling pattern on-site that resulted in a 1% increase in density. If this information is used to determine the optimal rolling pattern for the entire project, a conservative estimate would be a 10% increase in pavement life for a 14 mile stretch of Minnesota pavement.
MnDOT’s Plan:
- During mixture placement process, we use IR to measure compaction temperature to minimize mixture segregation (QC).
- During mixture compaction process, we use IC to ensure compaction uniformity (QC).
- Post compaction, we use GPR to assess HMA density to ensure compaction quality and uniformity, including longitudinal joint (QC and QA).
- Post compaction, we use Inertial Profilers to measure pavement smoothness to ensure a smooth pavement surface for ride and reduce vehicle dynamic impact on pavement (QA).
The above four elements will be a package of MnDOT quality control and assurance programs from mixture placement to post-construction. At each stage, a continuous and full coverage assessment method is used to ensure construction quality on the entire pavement surface.
Kyle and Shongtao presented this information at a concurrent session at last month’s TRB conference.