NRRA Newsletter: August 2019
DPS goes to North Dakota
At the beginning of July, Kyle Hoegh research project scientist for MnDOT and grad student Trevor Steiner went to North Dakota to demonstrate the Dielectric Profiling System. This was part of the ongoing outreach that is part of the NRRA’s mission: to provide technology transfer to other states and, in particular, our members.
The DPS combines specialized high-frequency ground penetrating radar with data-crunching software and calibration to create a map of recently constructed HMA. The map that is created by the system shows the density of the recently placed asphalt, which can tell the road owner if the job has been done right or not.
Hoegh’s goal is to get the DPS to correlate so accurately that cores will no longer be necessary. “It’s pretty self-explanatory that you don’t want to damage a pavement that you just placed. Until recently, however, that’s the only way we could make sure that it has the correct amount of compaction.”
In their first day in North Dakota, Hoegh was joined by Amy Beise, director of Materials & Research for the North Dakota DOT, and they ran the DPS over a new pavement near Castleton, ND.
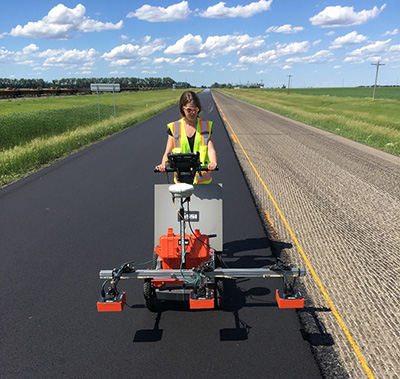 |
Amy Beise, from North Dakota Department of Transportation, collecting DPS data on ND18 near Casselton, ND. |
Beise gathered some of the data, and they took some cores and finally gathered mix. That last step is important because that’s where the dielectric gets converted to density for that specific pavement being tested. A gyratory compactor is then used to make asphalt specimens (pucks) with a wide range of air void content. The information from the pucks and an innovative way of measuring the dielectric of the pucks allows for calibration of the DPS data so it can be turned into the map of density and air voids in the pavement. This method based on puck measurements is becoming the key to gradually eliminating cores. In this case, rather than using field cores for calibration, they are only required sparingly to validate the conversion from dielectric to air void content is correct. After completing the DPS calibration and validation process, the density evaluation can be made based on tens of thousands of DPS air void content measurements as opposed to the current practice of using 2 cores for every 600 tons of placed pavement.
The second day of their demonstration took place in Fargo in a classroom, partially because it was raining. There Hoegh went over the data they gathered and showed the map it created.
Dale Heglund, program director for the Upper Great Plains Transportation Institute at North Dakota State University, attended the second day and said that the tool “did quickly point out areas that need attention, and it’s as near real time as you can get.” He added, “It doesn’t do any of us—owner or contractor—any good to get the information the day after. There’s no recourse.”
Doing quality control with cores means waiting for the asphalt to cool, drilling the core and then doing performance tests on it. In the best of circumstances, this takes at least 24 hours to get results and then it’s too late to change the pavement that’s already been installed.
The discussion on Day Two included DOT employees, academic researchers and contractors. “I was very impressed with how active and involved they were with the presentation, asking good questions and having a good discussion of what this technology would look like for them,” said Hoegh.
Heglund was impressed, saying “Kyle’s expertise has created enough confidence in the North Dakota group that we will be moving forward with this. It will make a reduction in field cores, which costs not only time and money, but it’s also safety issue for the coring crew.” He added, “North Dakota is confident in its decision to join the NRRA, but this demonstration pushed it so far out of the park. Wow.”
3D Milling Special Provision
Last month we had a link to a special provision for the Automated Machine Guidance (AMG) – Milling Method written by Rebecca Embacher, advanced materials technology engineer for MnDOT. MnDOT currently recommends the use of AMG milling when milling an existing asphalt surface for whitetopping and when using the existing asphalt pavement as a bond-breaker for an unbonded concrete overlay. As discussed last month, the AMG milling method allows for variable depth milling that helps address the varying in-place profiles, super elevations and crowns that are present in many of our roadways. Prior to use of this technology, corrections for these factors were achieved when paving the concrete and not during the milling operation. Consequently, this generated quantity overruns and negatively impacted pavement smoothness. All pavers perform best when operating at a consistent speed and placing a consistent depth of material. The AMG milling method creates the best opportunity to place a predictable amount of material in a uniformly smooth operation.
The AMG – Milling Method special provision says:
“The steering functions of the milling machine are operated by a contractor personnel, however, the milling operation is controlled by an onboard data acquisition system which automatically follows a Milling Surface Model to control variable depth milling based on inputs from robotic total stations.”
The “Model” was the topic of an all-day discussion of Building Information Modeling (BIM) at our recent Pavement Workshop. In short the model is an agreed-upon computer generated 3D representation of the project. With this model, says Embacher, you can do a simple pave-to-depth after the AMG milling operation.
Dale Harrington, with Snyder and Associates in Iowa, concurs and advocates a number of 3D modeling tools to save time, improve accuracy and save money on materials. He worked on a report titled Implementation Manual 3D Engineered Models for Highway Construction: The Iowa Experience from NRRA member the National Concrete Pavement Technology Center, Iowa State University. In this report, “it describes how the state of Iowa uses 3D engineered models for construction of highway projects, from planning and surveying through design and construction.” Iowa has been using variable 3D milling since 2003.
Harrington says most of the major contractors in Iowa have adopted 3D modeling (and milling) because it saves them so much time and money. The smaller contractors, he says, who haven’t accepted these new construction technologies are going to be at a competitive disadvantage now and in the future.
Accurate milling, he says, is important because it determines the profile of the road and, in turn, the quality of the paving. When the profile is good, the road surface doesn’t get too thin, risking failure, and is consistently smooth, which affects both the ride and overall performance of the road. Controlling thickness also helps control costs and overruns.
The future of 3D milling is now. With this special provision, it’s clear MnDOT is going in that direction. Embacher will be working with contractors to establish a roadmap for moving forward, as well as date to have this technology in place throughout Minnesota.
25 Years of Learning—MnROAD’s Anniversary Open House
In a few days we will be celebrating the 25th Anniversary Open House for MnROAD, taking place in August. Construction of this research facility was completed in August 1994, and over the years it has become one of the most important pavement research facilities in the U.S.
In recent years, the National Road Research Alliance has opened MnROAD’s research opportunities to other state DOTs and private companies.
“The people who support the mission of MnROAD drive the success of this state-of-the-art facility. The collaboration environment that it promotes facilitates a passion for learning and improving the sustainability of pavements.”
—Amy J. Beise, P.E., North Dakota Dept. of Transporation
“MnROAD is the premier proving ground for cold weather pavement innovation. The facility is top-notch and the team that supports it are the best of the best.”
—Dan Schellhammer, P.E., President, Midstate Reclamation and Trucking
“MnROAD has been a valuable resource for the Wisconsin Department of Transportation. Having a pavement test facility in a northern climate has been a tool that has provided great benefits to us. The research on low temperature cracking, understanding how freeze thaw conditions impact our designs, and being able to try new things in a heavily monitored and documented environment has been extremely useful.”
—Barry Paye, P.E., Chief Materials Engineer - Bureau of Technical Services, Wisconsin Dept. of Transportation
“For us, the best thing, besides access to data and sections, is how friendly, competent, and willing to help the staff are. MnROAD is definition of heaven for experimental researchers in pavements.”
—Soheil Nazarian, Univ. of Texas El Paso Center for Transportation Infrastructure
“The best thing about MnROAD is we are allowed to fail. We have a parallel stretch of interstate so if something goes really wrong all we have to do is switch traffic.”
—Matt Zeller, P.E., Executive Director, Concrete Paving Association of Minnesota
The open house will run from 9 a.m. to 3 p.m. Everyone is welcome. The day will include:
- Tours of the facilities and test tracks
- Equipment demos, many of which were invented at MnROAD
- Meeting past and current staff of MnROAD
If you have been part of that history, thank you. We hope to see you August 8, 2019.
Everyone is welcome throughout the day. If you plan to join us for lunch, please RSVP to lisa.bilotta@mn.state.us.
Pavement Research Resources