About this study
Project Overview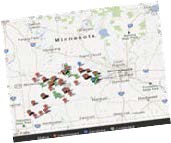
In 2013, MnDOT initiated a project in its District 8 region (twelve counties in southwest and west central Minnesota) to better understand freight customers’ transportation priorities and challenges and to incorporate their feedback into MnDOT’s planning and project development. A better understanding of these customers’ businesses and transportation needs is helping MnDOT to better align its work to support their success and, by extension, the economic vitality of the region and state.
The project identified concerns and suggested improvements in the areas of infrastructure, maintenance, communications and policy.
Manufacturers' Perspective Pilot Study Final Report - February 2014 (PDF)
Study Objectives
- To meet with freight transportation customers to better understand their perspectives and priorities for the transportation system and to improve MnDOT’s knowledge of Greater Minnesota industries that make the greatest use of the system and derive some of its greatest benefits.
- To systematically collect and analyze customer information to inform practical, near-term planning and operations, policy development and investment decision making.
- To build relationships among MnDOT, economic development professionals and freight transportation customers as a basis for both near term and ongoing transportation system improvement.
- To pilot a new process for soliciting and analyzing customer information—building relationships in the process—and determine its usefulness for future projects. This process included:
- Using a regional industry cluster approach to identify manufacturers important to the region’s economy;
- Creating interview teams comprised of MnDOT staff, University of Minnesota researchers and Extension staff, and local economic development professionals; and
- Hosting several internal and external engagement meetings to share mid-project findings.
- To support continuous improvement and develop recommendations for District 8 and statewide transportation systems and practices to better support freight transportation.
Project Highlights
The project’s cross-organization interview teams met with 60 manufacturers, 14 carriers and one distributor. The manufacturing firms represented a cross section of the region’s strongest industry clusters including processed food; agricultural products; information technology; building fixtures, equipment, services and heavy machinery.
The project team solicited input that would inform low cost/high benefit projects and technical assistance which can be accomplished in the one to four years, assuming available resources. Examples of manufacturer-requested improvements that have already been accomplished or are in program plans include:
1. Friendship Homes: This manufacturer of pre-fabricated homes wanted to retain and grow their market share in North and South Dakota and Canada by selling larger, 14-foot wide structures on par with their competitors from neighboring states. Expansion of their Montevideo plant to accommodate this construction was contingent upon permit approval to ship these oversized homes on Minnesota highways. The permit application was in process at MnDOT; however, District 8 staff connected with the permitting office to expedite the process, thereby cementing the business’ decision to conduct their $1 million expansion in the region. This expansion resulted in over 20 new jobs, according to the manufacturer’s general manager.
2. First District Association: This dairy cooperative, located in Litchfield, has deep roots in the region and supports over 1,000 jobs on its supplying farms. The association processes millions of pounds of milk each day. One of First District’s larger suppliers, located west of Willmar, ships milk to the First District processing plant every three hours, around the clock, 365 days per year. The flat topography and extreme winter weather in District 8 pose significant challenges to adhering to this shipping schedule. If roads are closed due to snow and ice events, and shipments aren’t delivered within a certain timeframe, the association literally has spilled milk.
Providing informal consultation, District 8 staff met with First District’s logistics staff to identify alternative routes in case of weather related closures along key routes. In addition, during extreme winter weather conditions, the supervisor in charge of plowing the dairy’s priority routes notifies the dairy when MnDOT plows are scheduled to pass so that the dairy’s trucks can follow behind the plows during blizzard conditions. This essentially no cost communication from MnDOT enables First District to receive their shipments safely, and with less waste, during the region’s extreme weather conditions.
3. Advance detour planning and communication: Many manufacturers and carriers indicated that detours can significantly affect their ability to efficiently transport freight, particularly oversized / overweight products. In response, District 8 revised its detour planning process so that instead of defining construction detours a few months ahead of projects, District staff initiated this planning a year ahead of construction. This allowed MnDOT to engage potentially affected residents and shippers to get their input a year ahead of time and plan detour routes that will enable manufacturers to more efficiently ship their products during construction season.
4. Construction updates and winter road conditions email distribution list: Another common theme from the feedback was that haulers need current, accurate information regarding construction projects and winter road conditions. MnDOT’s District 8 staff sent an invitation to manufacturers and regional economic development staff to join District 8’s email distribution list, which provides up-to-date information about projects, winter weather conditions and designated detour routes. Avoiding construction congestion and delays saves shipper and carriers time, fuel and maintenance costs and perishable input and product waste. Twelve manufacturers and carriers signed up for the notifications, not including those already on the list. In addition, District 8 is cross-walking all of the discrete items of input from interviews to existing construction and maintenance plans, to identify opportunities to address customers’ concerns. Ideas and improvements that could or would need to be implemented more broadly, e.g., improvements to 511mn.org, are being routed to and analyzed by appropriate MnDOT programs and staff.
Throughout the almost year-long project, the project team built in participation opportunities for internal and external stakeholders whose engagement was key to ensuring that the effort does not end as a point-in-time project but rather evolves into a continuous improvement process.